In this guide, we will explore various gate types, considerations for gate size, and best practices for gate design in injection molding processes.
What is a Gate in Injection Molding ?
Injection molding is a widely used manufacturing process for producing plastic parts with high precision and efficiency.
What is the Function of Gates in Injection Molds ?
The gate, a critical component in injection molding, controls the flow of molten plastic into the mold cavity.
Understanding Gate Types in Injection Molding
Valve Gate Injection Molding: Valve gates provide precise control over the flow of molten plastic into the mold cavity. They offer advantages such as reduced gate vestige and improved part quality.
Different Types of Gates: There are several gate types used in injection molding, including edge gates, fan gates, film gates, pin gates, and submarine gates, each offering unique benefits and applications.
Gate Vestige: Gate vestige refers to the residual mark or scar left on the molded part after the gate is removed. Proper gate design and placement can minimize gate vestige and improve part aesthetics.
Gate Size Determination: The size of the gate is crucial for controlling the flow rate of molten plastic and ensuring proper filling of the mold cavity. Factors such as part geometry, material viscosity, and mold configuration influence gate size determination.
Valve Gate Injection Molding: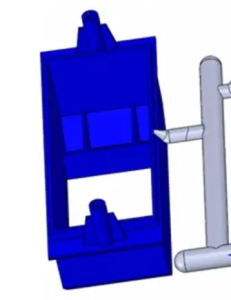
Valve gate injection molding employs a valve pin mechanism to precisely control the flow of molten material into the mold cavity. This technique ensures clean and controlled filling, minimizing gate vestige and producing high-quality parts with intricate details. By opening and closing the gate precisely, valve gate injection molding reduces material waste and enhances production efficiency, making it a preferred method for demanding applications.
Gate Vestige Injection Molding:
Gate vestige in injection molding refers to the residual mark left on the molded part after the gate is removed. Minimizing gate vestige is essential for improving part aesthetics and functionality. Techniques such as optimizing gate design, adjusting injection parameters, and utilizing advanced gate types can effectively reduce vestige, ensuring the production of flawless parts with consistent quality.
Gate Blush Injection Molding:
Gate blush occurs when the gate area of a molded part appears discolored or hazy due to improper injection molding conditions. It can be caused by inadequate cooling, excessive injection pressure, or polymer degradation. Controlling process parameters such as cooling rate, melt temperature, and injection speed is crucial for mitigating gate blush and ensuring uniform part appearance and quality.
Banana Gate Injection Molding:
Banana gate injection molding involves using a curved or banana-shaped gate design to facilitate material flow and reduce stress concentration. This gate configuration is particularly useful for parts with complex geometries or thin walls. By optimizing the gate shape and placement, banana gates improve mold filling and minimize defects, ensuring high-quality part production.
Cashew Gate Injection Molding:
Cashew gate injection molding employs a gate design resembling a cashew nut shape. This unique configuration is often used in multi-cavity molds to ensure balanced filling and reduce the risk of defects such as short shots or warping. By controlling material flow more effectively, cashew gates optimize production efficiency and enhance part quality in various injection molding applications.
Diaphragm Gate Injection Molding:
Diaphragm gate injection molding utilizes a thin, flexible membrane to control the flow of molten material into the mold cavity. This gate type offers precise gating control, minimizing gate marks and ensuring uniform part filling. Diaphragm gates are commonly used in applications requiring high part quality and intricate details, such as automotive components and consumer electronics.
Direct Gate Injection Molding:
Direct gate injection molding, also known as sprue gating, involves injecting molten material directly into the mold cavity through a single gate. This straightforward gating method is suitable for simple part geometries and can help streamline the molding process. Direct gating minimizes material waste and is often used in high-volume production runs where efficiency is paramount.
Disk Gate Injection Molding:
Disk gate injection molding utilizes a flat, disk-shaped gate design to control material flow into the mold cavity. This gate type offers uniform filling and minimizes gate vestige on the molded part. Disk gates are commonly used in applications requiring precise gating control and can help improve part quality by reducing flow-related defects.
Edge Gate Injection Molding:
Edge gate injection molding involves placing the gate at the edge of the part, allowing molten material to flow along the part’s perimeter. This gating method provides uniform filling and is suitable for parts with complex geometries or thin walls. Edge gates minimize gate marks and can help optimize production efficiency by ensuring consistent part quality.
Fan Gate Injection Molding:
Fan gate injection molding employs a gate design that resembles a fan, allowing molten material to spread out evenly as it enters the mold cavity. This gating method provides uniform filling and minimizes flow-related defects such as weld lines. Fan gates are commonly used in applications requiring precise gating control and can help improve part aesthetics and functionality.
Film Gate Injection Molding:
Film gate injection molding utilizes a thin, film-like gate design to control material flow into the mold cavity. This gating method offers precise gating control and minimizes gate vestige on the molded part. Film gates are commonly used in applications requiring high part quality and can help reduce material waste by optimizing material flow during the injection molding process.
Flash Gate Injection Molding:
Flash gate injection molding involves intentionally creating excess material at the gate area, which is then removed as flash during post-processing. This gating method is suitable for parts with large surface areas or complex geometries. Flash gates help prevent short shots and ensure complete cavity filling, resulting in high-quality molded parts with minimal defects.
Gate Freeze Injection Molding:
Gate freeze in injection molding refers to the premature solidification of molten material at the gate area, leading to flow restrictions and incomplete cavity filling. Gate freeze can be caused by factors such as inadequate cooling, excessive injection speed, or improper gate design. Controlling process parameters and optimizing gate geometry are essential for preventing gate freeze and ensuring smooth material flow during the injection molding process.
Gate Marks Injection Molding:
Gate marks in injection molding refer to visible blemishes or scars left on the molded part by the gate location. These marks can detract from part aesthetics and may indicate improper gating or processing conditions. Minimizing gate marks requires careful gate design, optimization of injection parameters, and proper part and mold design. By controlling material flow and optimizing gate geometry, manufacturers can reduce gate marks and produce high-quality molded parts.
Gate Seal Injection Molding:
Gate seal in injection molding refers to the closure of the gate after the completion of the injection phase, preventing material from flowing back into the runner system. A proper gate seal is essential for preventing drool or stringing and ensuring clean part ejection. Achieving an effective gate seal requires precise control of injection parameters and gate design, optimizing material flow and minimizing waste during the injection molding process.
High Gate Injection Molding:
High gate injection molding involves placing the gate at a higher elevation on the part, allowing molten material to flow downward into the mold cavity. This gating method provides uniform filling and minimizes flow-related defects such as weld lines. High gates are commonly used in applications requiring precise gating control and can help improve part aesthetics and functionality.
Hot Tip Gate Injection Molding:
Hot tip gate injection molding involves using a heated nozzle or gate insert to maintain the molten state of the material at the gate location. This gating method ensures smooth material flow and minimizes flow-related defects such as cold slugs or weld lines. Hot tip gates are commonly used in applications requiring high part quality and can help optimize production efficiency by reducing cycle times and material waste.
Injection Molding Gate Cutters:
Injection molding gate cutters are tools used to remove the gate from molded parts after the injection molding process. These cutters come in various shapes and sizes to accommodate different gate types and part geometries. Proper gate cutting is essential for achieving clean part surfaces and minimizing post-processing requirements. Injection molding gate cutters help improve production efficiency and ensure consistent part quality by facilitating precise gate removal during the manufacturing process.
Injection Molding Gate Defects:
Injection molding gate defects refer to issues that arise at the gate area during the injection molding process, leading to part quality issues or production inefficiencies. Common gate defects include gate vestige, blush, freeze, marks, and improper sealing. These defects can be caused by factors such as improper gating design, processing conditions, or material properties. Minimizing gate defects requires careful process optimization, gate design considerations, and regular quality control measures to ensure consistent part quality and production efficiency.
Injection Molding Gates and Runners:
Injection molding gates and runners are essential components of the injection molding process, responsible for delivering molten material from the injection unit to the mold cavity. Gates control the flow of material into the cavity, while runners distribute material throughout the mold. Proper gate and runner design is crucial for achieving uniform part filling, minimizing flow-related defects, and optimizing production efficiency. By carefully designing and optimizing gates and runners, manufacturers can ensure smooth material flow and produce high-quality molded parts with minimal waste.
Injection Molding Valve Gate:
Injection molding valve gate systems utilize a valve pin mechanism to control the flow of molten material into the mold cavity. This gating method offers precise gating control, minimizing gate vestige and ensuring uniform part filling. Valve gate systems are commonly used in applications requiring high part quality and can help optimize production efficiency by reducing cycle times and material waste.
Pin Gate Injection Molding:
Pin gate injection molding involves using a pin-shaped gate design to control material flow into the mold cavity. This gating method offers precise gating control and is suitable for parts with intricate geometries or tight tolerances. Pin gates minimize gate vestige and can help improve part quality by ensuring uniform filling and reducing flow-related defects.
Pin Point Gate Injection Molding:
Pin point gate injection molding utilizes a pin-shaped gate design with a sharp point to control material flow into the mold cavity. This gating method offers precise gating control and minimizes gate vestige on the molded part. Pin point gates are commonly used in applications requiring high part quality and can help reduce material waste by optimizing material flow during the injection molding process.
Side Gate Injection Molding:
Side gate injection molding involves placing the gate on the side of the part, allowing molten material to flow directly into the mold cavity. This gating method offers uniform filling and minimizes flow-related defects such as weld lines. Side gates are commonly used in applications requiring precise gating control and can help improve part aesthetics and functionality.
Design Considerations for Injection Molding Gates
Gate Location: Gate placement plays a significant role in part quality and mold design. Careful consideration should be given to gate location to ensure uniform filling and minimize flow-related defects.
Gate Design: The design of the gate, including its shape, size, and orientation, affects part quality, cycle time, and mold longevity. Common gate designs include direct gates, diaphragm gates, and disk gates, each with specific advantages and limitations.
Gate Defects: Gate-related defects such as gate blush, gate freeze, and gate marks can affect part aesthetics and functionality. Proper gate design and maintenance are essential for preventing these defects.
how to determine gate size injection molding?
Determining the ideal gate size in injection molding is pivotal for achieving top-notch part quality and operational efficiency. This process begins with a thorough assessment of the part’s design, material properties, and intended application. Calculating material flow dynamics, considering factors like viscosity and mold temperature, guides the selection of gate location(s) where flow lines converge. Gate types, such as edge gates or fan gates, are then chosen based on these considerations. The gate size itself is meticulously calculated, factoring in injection speed, pressure requirements, and cavity volume. Achieving a balanced fill rate throughout the cavity is imperative to avoid defects. This iterative process often involves trial-and-error adjustments, supported by consultations with experts and, if necessary, real-world testing. By comprehensively considering part geometry, material behavior, and production needs, the optimal gate size can be determined to ensure seamless injection molding processes and impeccable part quality.
Best Practices for Gate Design and Size
Optimize Gate Size: Properly sizing the gate is crucial for achieving optimal part quality and production efficiency. Gate size should be determined based on mold flow analysis, material properties, and part specifications.
Consider Gate Cutters: Gate cutters are used to remove gates from molded parts cleanly and efficiently. Choosing the right gate cutter design and placement can minimize post-processing and improve part aesthetics.
Gate Troubleshooting: Understanding common gate-related issues and their root causes is essential for troubleshooting injection molding processes. Techniques such as gate freeze studies and valve gate troubleshooting can help identify and address gate-related issues effectively.
Conclusion
Gate design, size, and placement are critical factors in the success of injection molding processes. By understanding the different types of gates, considerations for gate size, and best practices for gate design, manufacturers can optimize part quality, production efficiency, and overall process performance in injection molding operations.