Precision Plastic Injection Molding Services
Turn your ideas into reality with high-quality, cost-effective solutions.
Why Choose Our Plastic Injection Molding Service?
ISO9001
ISO 9001:2015 | ITAR Registered
Precision, Every Time
From the first mold to mass production, we prioritize accuracy in every detail. Our injection molding process guarantees consistent, flawless parts with tight tolerances so you can trust each product will match your vision precisely.
Fast and Scalable Production
Get to market faster with our streamlined, high-output systems. We offer rapid prototyping and scalable production that grows with you, whether you need a short production run or millions of units.
Cost-Efficient Manufacturing
Reduce waste and lower your per-part costs. Our advanced technology optimizes material use and speeds up cycle times, giving you cost-effective manufacturing without compromising quality.
Broad Material Selection
Choose the perfect material for your application. We offer a wide range of thermoplastics, from ABS and polypropylene to high-performance polymers, ensuring you get the ideal mix of durability, flexibility, and aesthetic appeal.
DTG Injection Molding Process
For simple parts, product lead times can be reduced to as little as 3 days.Upload your part to see if it qualifies.
01
Quote Phase
02
Prototype & Testing
03
Production
04
Logistics & Delivery
Why Work With Us?
- Trusted Expertise: Decades of experience in the industry.
- Cutting-Edge Technology: State-of-the-art machinery and software.
- Sustainability: Minimizing waste with eco-friendly practices.
- End-to-End Service: From design to delivery, we handle every detail.
Custom Injection Molding: Tailored to Your Needs
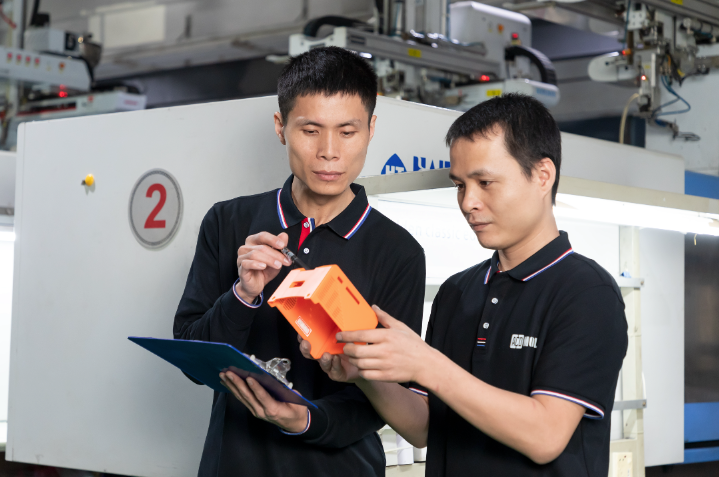
Industries We Serve
Whether it’s automotive, healthcare, electronics, or consumer goods, our plastic injection molding services are trusted across industries. We handle projects of any complexity and scale, offering a tailored solution to meet your specific needs.
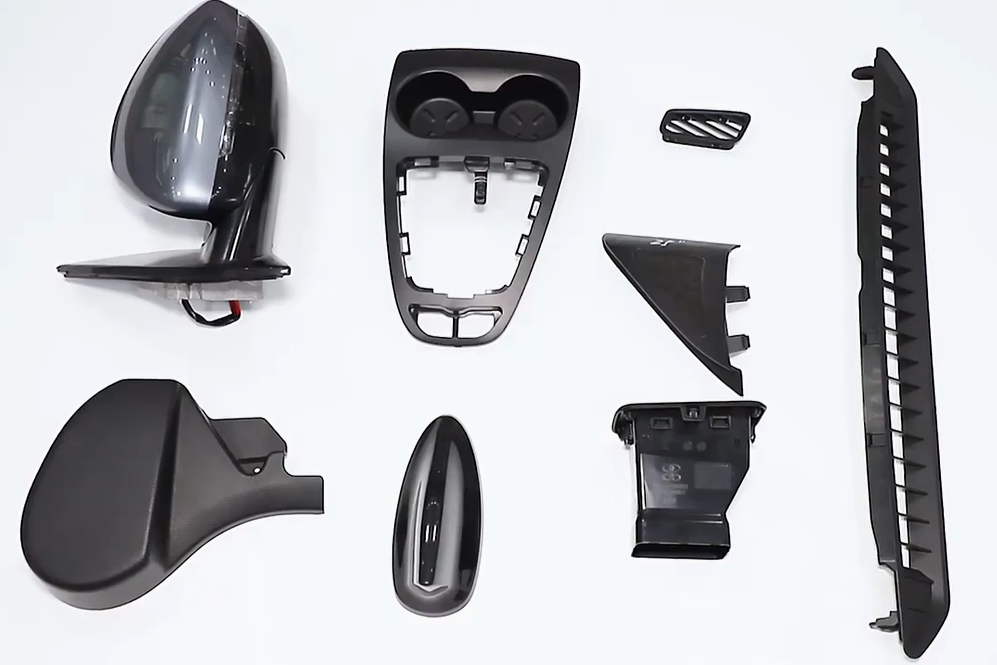
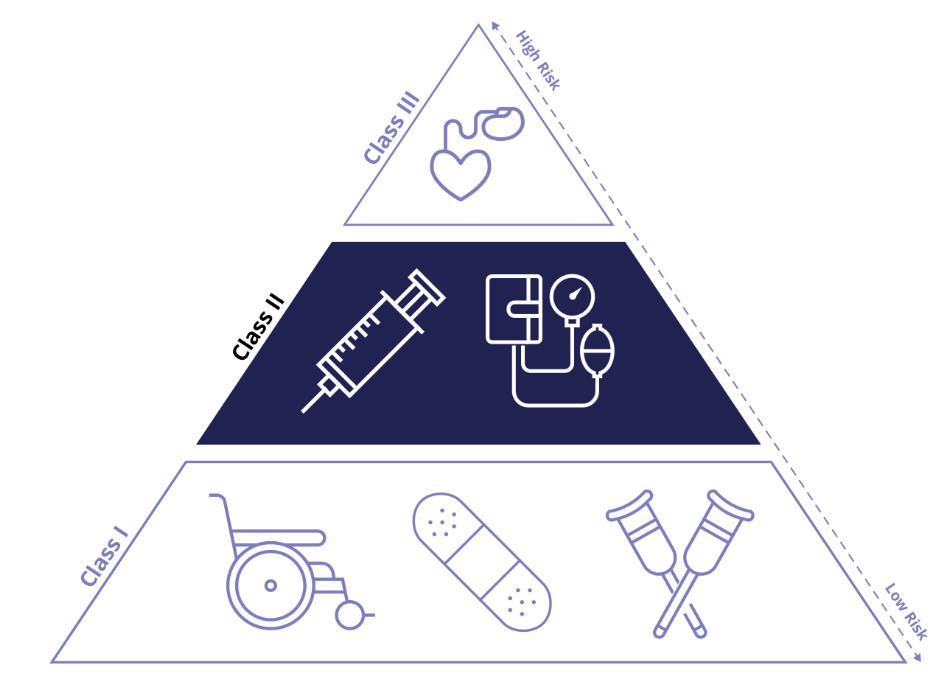
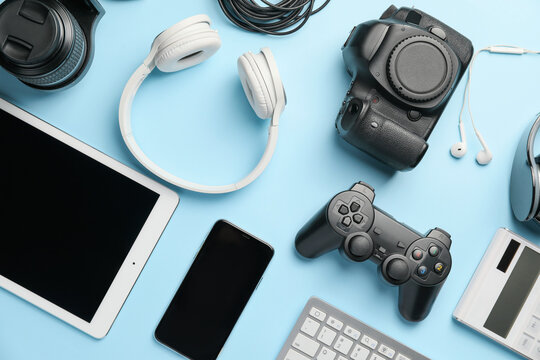
Our Comprehensive Plastic Injection Molding Services
Experience the DTG Advantage: Our injection molding process combines state-of-the-art technology, stringent quality control, and industry-specific adaptability, offering a superior alternative to standard offerings in the market.
Other injection molding factories
- Unable to design moulds
- Only provide injection molding
- Complex communication
- Mould issues require back-and-forth communication
- Slow response
- Time-consuming
Our injection molding service
- One-stop service
- Capable of both injection molding and mould design
- Surface treatment, Assembly & Packaging
- Saving communication and transportation costs
- Quick response
- Cost-effective for customers
- Saves mould costs
Additional Molding Options Available at DTG
Insert Injection Molding
Insert injection molding is a manufacturing process that incorporates pre-formed inserts, such as metal or plastic components, into a molded part, enhancing strength and functionality.
Overmolding Service
Overmolding injection molding is a technique that combines multiple materials into a single component, enhancing functionality and durability through the application of a second layer over an existing part.
Appliance Injection Molding Service
Appliance injection molding service specializes in producing high-quality, durable plastic parts for various household appliances using advanced injection molding techniques.
Aerospace Injection Molding Service
Aerospace injection molding service offers specialized manufacturing of lightweight, high-performance components for the aerospace industry, ensuring compliance with stringent safety and quality standards.
Rubber Injection Molding Service
Rubber injection molding service provides precise and efficient manufacturing of rubber components using high-pressure injection techniques.
Low-Volume Injection Molding Service
Low-volume injection molding service provides cost-effective production of small quantities of customized plastic parts, ideal for prototyping and niche applications.
China Injection Molding Service
China injection molding service delivers high-quality, cost-efficient manufacturing of plastic components, leveraging advanced technology and extensive industry expertise.
Surface Finish Options
Draft angle requirements will vary by requested finish. Industry standard Mold-Tech finishes are also available.
DTG offers any type of SPI surface finish, such as A-1, D-2 or D-3.
Finish | SPI* standard | Finishing Method | Typical surface roughness Ra (μm) |
---|---|---|---|
Super High Glossy finish | A-1 | Grade #3, 6000 Grit Diamond Buff | 0.012 to 0.025 |
High Glossy finish | A-2 | Grade #6, 3000 Grit Diamond Buff | 0.025 to 0.05 |
Normal Glossy finish | A-3 | Grade #15, 1200 Grit Diamond Buff | 0.05 to 0.10 |
Fine Semi-glossy finish | B-1 | 600 Grit Paper | 0.05 to 0.10 |
Medium Semi-glossy finish | B-2 | 400 Grit Paper | 0.10 to 0.15 |
Normal Semi-glossy finish | B-3 | 320 Grit Paper | 0.28 to 0.32 |
Fine Matte finish | C-1 | 600 Grit Stone | 0.35 to 0.40 |
Medium Matte finish | C-2 | 400 Grit Stone | 0.45 to 0.55 |
Normal Matte finish | C-3 | 320 Grit Stone | 0.63 to 0.70 |
Satin Textured finish | D-1 | Dry Blast Glass Bead #11 | 0.80 to 1.00 |
Dull Textured finish | D-2 | Dry Blast #240 Oxide | 1.00 to 2.80 |
Rough Textured finish | D-3 | Dry Blast #24 Oxide | 3.20 to 18.0 |
As machined | – | Finished to the machinist’s discretion | 3.20 (with visible machining marks) |
*SPI (Plastics Industry Trade Association) standards
What is Plastic Injection Molding?
Injection molding is a manufacturing process that consists of filling a metal mold cavity with liquid plastic resin, which then cools and forms a plastic part.
It’s most often used for the manufacturing plastic parts at scale due to its low material waste and low cost per part. It’s an ideal manufacturing process for industries like medical devices, consumer products, and automotive.
Our plastic injection molding process produces custom prototypes and end-use production parts with lead times as fast as 1 day. We use aluminum molds that offer cost-efficient tooling and accelerated manufacturing cycles, and stock about 200 different thermoplastic resins.
Common applications for plastic injection molding:
- low-volume production
- bridge tooling
- pilot runs
- functional testing and prototyping
The key steps in injection molding:
- Clamping: The mold’s two sides are sealed shut under hydraulic pressure.
- Screw Recovery: Plastic material is fed into the barrel and conveyed via rotating screw down the barrel toward the front of the screw. As the material is conveyed it is heated to the specified melt temperature creating the “shot” or volume of material to be injected.
- Injection: Screw is pushed forward injecting the material under very high pressure into the mold.
- Cooling: Water circulated through channels in the mold to remove heat and solidifies the molded part.
- Ejection: The clamp releases, mold opens and part is ejected from the mold.