Achieving optimal validation in injection molding involves ensuring that the molded parts meet all specified requirements and quality standards throughout the production process. Validation ensures that the injection molding process consistently produces parts that conform to design specifications and performance criteria. Here’s a detailed guide on how to achieve optimal validation in injection molding:
1. Define Validation Requirements
- Specifications and Standards:
- Clearly define the required specifications, quality standards, and performance criteria for the molded parts.
- Specify dimensional tolerances, material properties, surface finish requirements, and functional performance criteria.
- Regulatory Compliance:
- Ensure compliance with industry regulations, standards (such as ISO 9001), and customer-specific requirements.
- Understand any regulatory requirements related to the application of the molded parts (e.g., medical, automotive, aerospace).
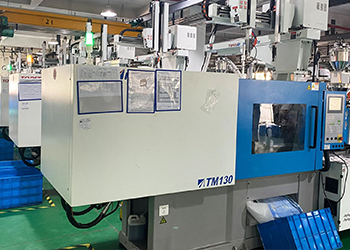
Choose us for your custom injection molding needs and experience excellence in every detail. Our China-based factory provides innovative solutions, competitive pricing, and fast turnaround times. Get your custom quote now!
2. Design and Development Phase
- Design for Manufacturing (DFM):
- Collaborate with design engineers to optimize part designs for injection molding.
- Consider factors such as draft angles, wall thickness uniformity, gating location, and parting line design to facilitate moldability and consistent quality.
- Prototyping and Testing:
- Develop prototypes to validate part designs and mold functionality.
- Conduct initial testing to evaluate dimensional accuracy, material properties, and functional performance of prototype parts.
3. Mold and Tooling Preparation
- Mold Design and Construction:
- Design molds with appropriate features (e.g., cooling channels, venting, ejector systems) to ensure consistent part quality and dimensional stability.
- Use high-quality materials and machining techniques to construct durable molds that can withstand repeated molding cycles.
- Tooling Validation:
- Validate the mold design through simulations (e.g., mold flow analysis) and prototype tooling trials.
- Ensure that the mold design allows for proper filling, packing, and cooling of the material to prevent defects.
4. Process Validation
- Process Development:
- Develop an injection molding process that optimizes parameters such as injection speed, pressure, temperature profiles, and cooling time.
- Conduct DOE (Design of Experiments) studies to identify optimal process settings that minimize variability and ensure part consistency.
- First Article Inspection (FAI):
- Perform FAI to verify that the initial production parts meet all specified requirements and quality standards.
- Inspect dimensional accuracy, surface finish, material properties, and functional performance of the molded parts.
5. Production Validation
- Process Monitoring and Control:
- Implement process monitoring systems (e.g., statistical process control, real-time monitoring) to continuously monitor key process parameters.
- Establish control limits and conduct regular process audits to ensure adherence to validated process parameters.
- Verification and Validation (V&V):
- Conduct periodic verification and validation activities to confirm that the injection molding process consistently produces parts that meet the required specifications.
- Use statistical analysis (e.g., capability studies, process capability indices) to quantify process performance and capability.
As a leading mold injection manufacturer in China, we deliver superior molds for various industries. Our state-of-the-art facilities and expert team ensure top-notch quality and timely delivery. Contact us now for a competitive quote!
6. Documentation and Traceability
- Documentation:
- Maintain comprehensive documentation of validation activities, including mold designs, process parameters, inspection results, and corrective actions.
- Ensure traceability of parts back to their production batches and associated validation records.
- Change Control:
- Implement a change control process to manage any modifications to molds, materials, or process parameters that may impact part quality and validation status.
- Perform re-validation or qualification activities as necessary following any significant changes.
7. Continuous Improvement
- Root Cause Analysis:
- Investigate and address any deviations, non-conformities, or quality issues through systematic root cause analysis (e.g., 5 Whys, fishbone diagrams).
- Implement corrective and preventive actions (CAPA) to prevent recurrence of issues and improve process reliability.
- Feedback Loop:
- Solicit feedback from stakeholders (e.g., production team, quality assurance) to identify opportunities for process optimization and enhancement.
- Continuously update validation protocols and procedures based on lessons learned and industry best practices.
Conclusion
Achieving optimal validation in injection molding requires meticulous planning, rigorous testing, and continuous monitoring of key process parameters. By following a structured approach from design and development through to production and continuous improvement, manufacturers can ensure that injection molding processes consistently produce high-quality parts that meet customer expectations and regulatory requirements.
Related Conten: Plastic Parts Manufacturer