When plastics are revealed to the ultraviolet radiation created by the sunlight, they either absorb it or produce free radicals that negatively influence the material’s mechanical residential or commercial properties. In addition to a decrease in mechanical stamina, exposure to UV radiation can generate the following impacts on plastics with reduced UV resistance:
- A chalk-like surface area look
- Embrittlement and splitting on the surface
- Shade changes/fading– to see just how 3D-printed plastics stand up to severe UV exposure, look into DTG’s “Will It Fade?” video
It needs to be noted that there is a distinction between UV-resistant plastics and UV-stabilized plastics. Those that are naturally resistant to UV destruction are described as UV-resistant plastics. The ones that do not normally stand up to degradation call for various additives to enhance their UV resistance and are called UV-stabilized plastics. Neither polypropylene neither nylon is naturally resistant to UV, so they need ingredients.
UV Resistance of Polypropylene vs Nylon
In their natural states, both polypropylene and nylon are negatively affected by exposure to UV radiation, so they are not known as UV-resistant plastics. Their reactions to UV radiation are defined below.
Impacts of UV Radiation on Polypropylene
Polypropylene is very prone to degradation by UV radiation in its base type (i.e. no pigment or ingredients). The product comes to be brittle after extended exposure. In fact, fundamental polypropylene can shed as much as 70% of its mechanical stamina after 6 days well worth of direct exposure to high-intensity UV radiation. It ought to be kept in mind, nevertheless, that even with the additives, polypropylene will certainly still degrade relatively rapidly when revealed to sunlight for a prolonged period of time.
Polypropylene is sensitive to ultraviolet wavelengths of 290-300, 330 & 370 nm (nanometers). These are thought about the spectra maxima of polypropylene.
Even though polypropylene has wonderful mechanical stamina and is highly chemically resistant, it is not fit for prolonged direct exposure to sunlight. Polypropylene is likewise hard to layer so it’s ideal to merely maintain this material out of straight sunshine completely.
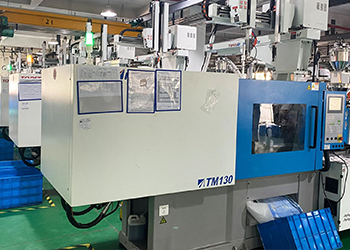
Choose us for your custom injection molding needs and experience excellence in every detail. Our China-based factory provides innovative solutions, competitive pricing, and fast turnaround times. Get your custom quote now!
Impacts of UV Radiation on Nylon
Nylon is vulnerable to deterioration by UV radiation, however not all nylons coincide. Nylon 6, as an example, is extra resistant than nylon 6/6. The color of nylon components will certainly tend to discolor over time when subjected to UV. Nylon breaks down using the very same device as polypropylene– the radiation produces complimentary radicals that better break down intermolecular bonds.
Nylon is sensitive to UV radiation in the wavelength series of 290-315 nm. Again, this is called the product’s ranges maxima.
Nylon is an extremely durable and versatile product that’s wonderful in products that get revealed to moisture. If modest exposure to UV radiation is expected, nylon 6 or nylon 12 are good alternatives. However, continual direct exposure to UV radiation will cause accelerated degradation.
Improving UV Resistance
While nylon and polypropylene are not usually seen as UV-resistant plastics, specific additives can boost their efficiency. These additives take the type of stabilizers, absorbers, or blockers.
- Blockers – Fillers like titanium oxide or carbon black pigments can function as UV radiation blockers. These pigments assist stop the UV rays from reaching the plastic’s actual polymers and hence lengthen the material’s lifespan.
- Absorbers – Absorbers function by soaking up UV radiation and afterwards converting it into warmth. Common natural absorbers consist of benzophenones and benzotriazoles. Benzotriazoles can be introduced in concentrations as reduced as 0.5% by volume and still dramatically enhance UV resistance.
- Stabilizers – Stabilizers function by trapping any free radicals that obtain developed. This then reduces subsequent deterioration of the intermolecular bonds within the plastic. Stabilizers are likewise known as scavengers due to the fact that they “feed on” and collect any kind of free radicals. Amongst the most common are the hindered amine light stabilizers (HALS).
Sometimes, all 3 kinds of additives are presented into the plastic to improve its UV resistance on numerous fronts.