Injection molded parts are often marked with a material code, but it is not always a requirement. The use of material codes can depend on industry standards, regulatory requirements, and company policies. Here’s an overview of why material codes are commonly used and when they might be required:
Reasons for Using Material Codes on Injection Molded Parts
1. Identification and Traceability
- Material Identification: Material codes help identify the type of plastic used in the part, which is important for recycling, repair, and replacement purposes.
- Traceability: Codes allow for better traceability of parts, aiding in quality control and compliance with industry standards.
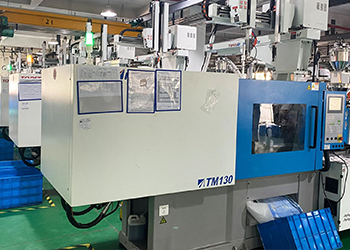
Choose us for your custom injection molding needs and experience excellence in every detail. Our China-based factory provides innovative solutions, competitive pricing, and fast turnaround times. Get your custom quote now!
2. Regulatory Compliance
- Recycling Requirements: In many regions, regulations require plastic products to be marked with material codes to facilitate recycling. For example, the Resin Identification Code (RIC) system is widely used in the United States.
- Industry Standards: Some industries have specific standards that mandate the use of material codes to ensure compatibility and safety. For example, automotive and medical device industries often have stringent requirements.
3. Quality Control
- Manufacturing Consistency: Material codes help manufacturers ensure that the correct material is used for each part, maintaining consistency and quality.
- Batch Identification: Codes can also include information about the batch or lot, which is useful in tracking and resolving any quality issues.
4. Customer Information
- End-User Guidance: Providing material information helps customers understand the properties of the product, such as its durability, chemical resistance, and suitability for certain applications.
When Material Codes Might Be Required
1. Regulatory and Industry Standards
- Mandatory Marking: Some regulations and industry standards mandate material codes on plastic parts. For instance, food-contact plastics and medical devices often require specific markings to ensure safety and traceability.
2. Company Policies
- Internal Standards: Many companies adopt internal policies that require material codes to streamline their production and quality assurance processes.
3. Recycling and Environmental Initiatives
- Sustainability Efforts: Companies committed to sustainability and recycling often include material codes to support recycling programs and reduce environmental impact.
Common Material Codes
1. Resin Identification Code (RIC)
- Numbers 1-7: This system uses numbers to identify different types of plastics, such as PET (1), HDPE (2), PVC (3), LDPE (4), PP (5), PS (6), and other plastics (7).
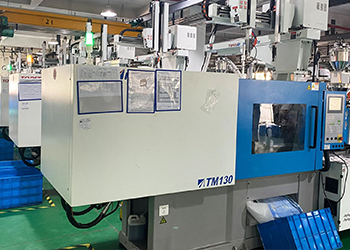
Choose us for your custom injection molding needs and experience excellence in every detail. Our China-based factory provides innovative solutions, competitive pricing, and fast turnaround times. Get your custom quote now!
2. ISO and ASTM Standards
- ISO Codes: The International Organization for Standardization (ISO) provides standards for marking plastics.
- ASTM Codes: The American Society for Testing and Materials (ASTM) also has standards for identifying plastic materials.
3. Custom Codes
- Company-Specific Codes: Some companies use custom codes that provide more detailed information, such as the specific grade of plastic or additional additives used.
Conclusion
While not universally required, material codes on injection molded parts are commonly used for identification, traceability, regulatory compliance, quality control, and customer information. The necessity of these codes depends on the specific regulations, industry standards, and company policies governing the production and use of the parts. Marking parts with material codes can significantly enhance recycling efforts, maintain quality, and ensure proper use and safety of the products.
Related Conten: Rapid Injection Molding